WORKS
導入事例

ジャパンセミコンダクター
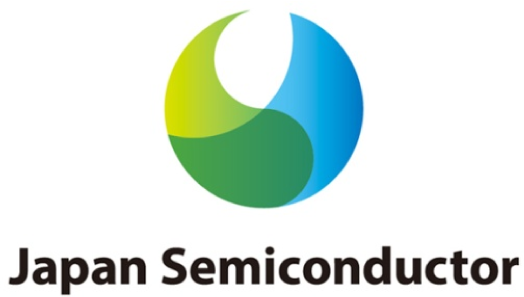
株式会社ジャパンセミコンダクター 大分事業所様
屋内測位の活用で大規模半導体工場世界NO.1の生産効率を目指す
~新生ジャパンセミコンダクター「人の見える化」によるスマート工場の構築~
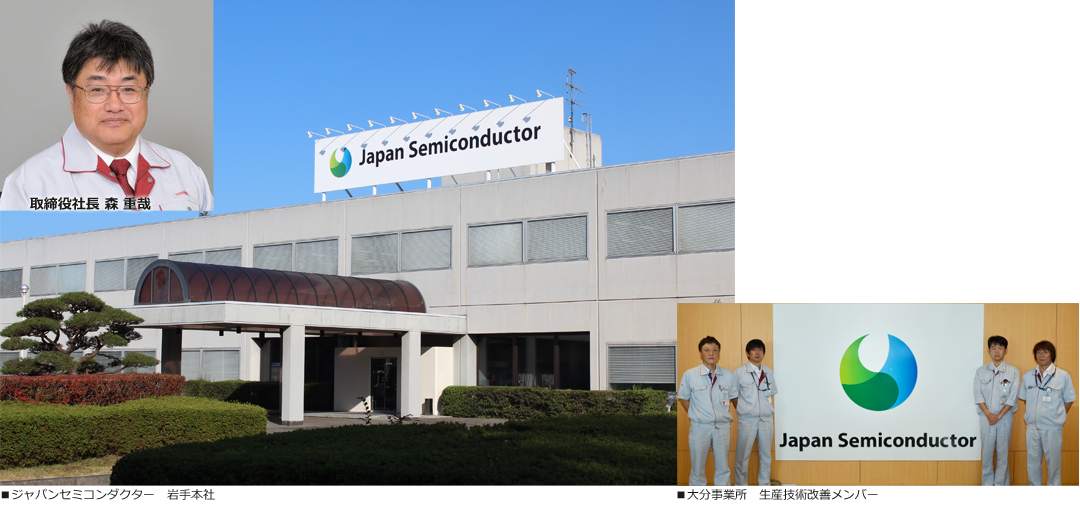
株式会社ジャパンセミコンダクター大分事業所では、少量多品種かつ工程数が多い半導体製造の現場において、「人の見える化」が課題とされていた。 同社ではBLEBeacon による屋内測位で人の動きを可視化・分析する「iField indoor」を導入、「人の見える化」を実現、さらにモノや設備の情報を重畳した「M 3 Vision モニター」を構築、最適かつフレキシブルな人員配置を実現した。 人の動きの改善による損失の解消から、「スマート工場」の実現により、大規模半導体工場世界NO.1 の生産効率を目指す同社の取組をレポートする。
大分工場の課題とその解決提案
半導体はクリーンルーム( 以下CR )と呼ばれる、清浄度の高い部屋で生産される。大分事業所では作業者がシフト制で 24時間連続稼働の生産を行っているが、CRはマニュアルで運用されており、人の動きが製造コストに直結する。
半導体は製造工程が多く(ある代表製品例にとると工程数は300近く)、また製造方法が個々の製品により微妙に異なり、機器の設定も違うなど工期やロットが多様である。
これまで同事業所ではさまざまな生産技術改善取組を行ってきており、2007年〜 2012年までに2倍の作業効率改善( 人員半減化)は達成されているが、時間帯や個人によるバラツキやムリ・ムダ・ムラなどは解消されず、1日あたり20万超の損失が発生しており、「人の見える化」は急務であった。
問題は人員配置にあった。これまでは、育成業務や労務の観点などから、作業者を工程毎の部屋での固定した業務形態が採用されており、全体に目が行き届きにくい体制だったことで、同一時間帯でも工程によって人員不足(人待ち工程)と人員余剰(手待ち工程)が発生していた。
この解決のためには状況に応じた流動的な人員の適所配置(余剰工程→不足工程)が必要であり、事業所内でのリアルタイムな「人の見える化」に取り組むこととなった。
この取り組みで以下2点の実現を目標とした。
1.人待ち工程・装置を把握しながらも人員の所在不明により発生していた機会ロス改善のため、リアルタイムなモニタにより全作業者を所在把握し、最適配置・作業指示を可能にする。
2.作業数に対し労働時間のばらつきが非常に大きく、工程により人待ち、手待ちが発生していた点を改善するため、オンライン測位データから個人別・工程毎に稼働率を算出し、データ分析することで課題の顕在化、改善対策を行う。
iField indoor で「人を見える化」する
同社では「人の見える化」実現のために「iField indoor 」を採用した。「iField indoor 」は、BLE Beacon を使うことで屋内測位を可能にし、可視化・分析まで行えるソリューションである。
大分事業所内の全棟にわたり、建物内部に2500個のBLE Beacon を設置し、スマートフォンを随時100台稼働させて作業者の位置を測位することで、作業員の位置情報の「リアルタイム見える化」が実現した。また、稼働率算出のためのデータ( 歩行・作業・待ち、歩数・速度etc )取得に成功した。
CR内の屋内測を全面導入し、「人のものさし」(稼働率)を作る取組は他に類を見ない。
「iField indoor 」の導入は、既存システムと融合が可能であった点が決め手となった。
製品の機密性が高い点や、これまで蓄積したモノや設備の稼働状況も合わせて活用できるためだ。
これまで取り組んできた「モノ・設備」のリアルタイム情報に「人」を加えたことで、工場マップ上に全ての情報がリアルタイムに描画できる「M 3 Vision モニター」が実現したのである。
「スマート工場」の実現で世界No1生産効率を目指す
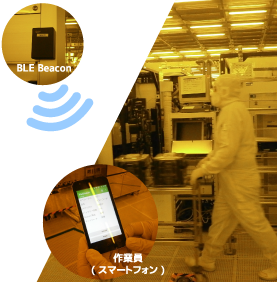
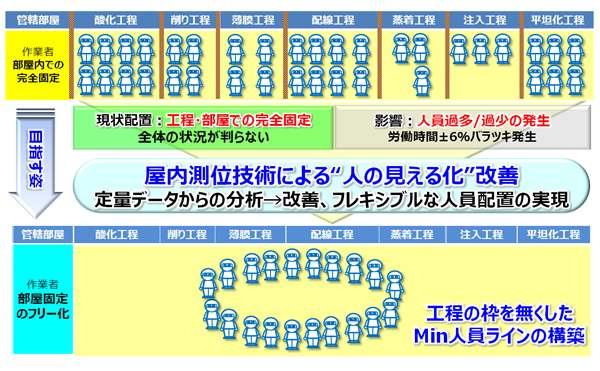
リアルタイムモニタ実現により、人員の最適配置に段階的に取り組むことが可能になった。現在はその第1段階として、セミオート指示化に取り組んでいる。リアルタイムモニタと自社で開発したフリーOPガイドモニタ(工程ごとの人待ちを把握できるシステム)を使い、管理者が各々の画面を見ながら、人待ち工程から手待ち工程へ人員を移動する。
これにより人待ち率を4%削減することに成功した。この段階では、各作業者のスキルをシステムに加味していなかったが、次回の実証では、「オンライン多能工(スキル)Map 」を構築・機能追加して運用することにより、さらに人待ち率を削減できる見込みだ。
また、従来装置のイベント(トラブル・チョコ停・回収など作業者の処置が必要な場合)もリアルタイムにウェブ上で把握し、装置の近傍にいる作業者に対してダイレクトに指示を出す仕組みを開発し、9月より運用を開始している。
従来は工程・部屋単位での完全固定の人員配置であったため、人員の過多/過小により労働時間換算で損失が発生していたが、屋内測位技術による「人の見える化改善」により、定量データでの分析からフレキシブルな人財配置を実現することで、損失改善の取組が進んでいる。
今後は測位データを基に、工程の枠にとらわれず手待ち人員を人待ち工程へ最適配置を行うことで、人財としての付加価値向上を図っていく。工程の枠をなくした人員ミニマムラインを構築することで、17年度末には現状労務費から10%削減を目標に注力していく。
さらに既存の取組との融合により、「スマート工場」( IoT化による生産革新を実現する次世代型工場)の構築を目指し、ビジネスチャンスを拡げていく。
ジャパンセミコンダクター大分事業所の生産技術改善メンバーは「改善にbestは無く、better=より良くなる改善に取組み、200mm半導体工場として世界No1の生産効率を目指し、お客さまに『高品質・低価格・短納期』の製品を提供できるモノづくり力を身につける」と力強く語った。
(2016年8月取材)
システムのポイント
- BLE Beaconを使った屋内測位技術を採用
- 国内製造工場初の屋内測位システムの全面導入
- 人待ち率を4%削減に成功、現状労務費から10%削減を目標
お客様プロフィール
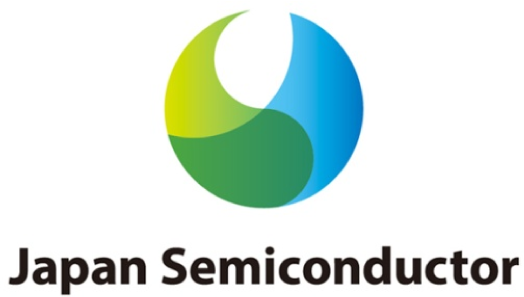
株式会社ジャパンセミコンダクター
2016年4月1日に、東芝大分工場と岩手東芝エレクトロ二クスを融合し設立された半導体製造工場。従業員数は約2200名。
大分事業所は、1970年に東芝大分工場として創業。製造主力製品は、エアーバッグやエンジン制御等で使われるMixed signal IC, カーオーディオやカーナビ等で使われるMCU/ASICを中心とした車載製品。その他にもセンサー製品など幅広く生産・製造しています。